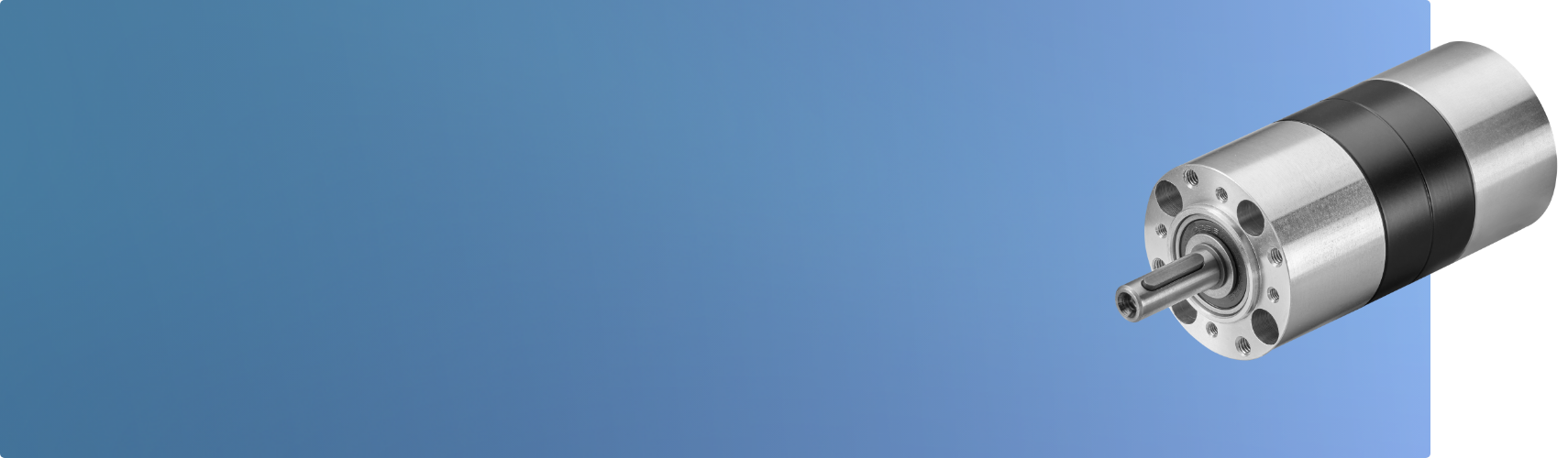
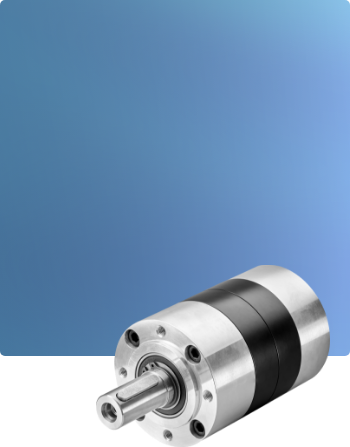
What Is a Planetary Gear?
A planetary gear (also: epicyclic gear) is a technical design that serves as a “link” for power transmission between a drive source (the motor) and an application to be moved (e.g. the movement of a wheel). For many decades, we from IMS Gear have been renowned experts for the design and manufacturing of planetary gears for a great variety of industrial applications.
Where Are Planetary Gears Used?
The advantage of planetary gears is their ability to combine high power density with little installation space. A further important factor is the low noise emission that can be realized by the specific design. This makes planetary gears an ideal solution for a great variety of applications, e.g.
- logistics (industrial trucks, driverless transport vehicles, ...)
- building technology (e.g. automated access systems, barriers and doors), household devices (e.g. robot lawn mowers, appliances, ...)
- agricultural technology / farming (e.g. feeding and milking robots, seed drills, ...)
- and many more.
How Does a Planetary Gear Work?
Basically, planetary gears work as the name implies: the sunwheel is in the center and driven by the motor. It confers its motion to three rotary planetary wheels which form a stage. They are arranged on the bearing bolts of a planetary carrier. The last planetary carrier is rigidly connected to the drive shaft and so provides power transmission at the output. On the outside, the planetary gear wheels rotate in a gearbox with internal gearing, the so-called ring gear.
Input and output are arranged coaxially with planetary gears, the shafts rotate in the same direction. PLGs are suitable for clockwise and counter-clockwise rotation, alternating, continuous and intermittent operation and are characterized by a high level of efficiency. The compact design offers high power density compared to other gear designs and high torque transmission for extremely small installation space.
If the number of teeth of the sun wheel and planetary wheels is changed, different gear reductions are possible within one stage. We from IMS Gear combine the reductions of our planetary gears in up to four stages. In this way, an enormous variety of different gear requirements can be realized.
Why Is the Output Torque of a Planetary Gear so Important?
Output torque is the most important parameter when choosing a planetary gear. The gear reduction reduces the relatively high rotational speed of the motor (rpm), delivering a lower rotational speed at the output end. This increases the output torque in inverse ratio. To link the planetary gear to the respective application a specific connecting flange is required.
As different manufacturers apply different measuring methods, great care must be taken when seeking to make a comparison. We will be pleased to calculate the maximum axial and radial load for your specific application under consideration of all parameters. Higher loads can be achieved through design measures. We will be happy to develop tailor-made implementation concepts for our customers.
Which Motors Can Planetary Gears Be Adapted to?
The connection between driving shaft (the motor) and the planetary gear is highly individual as there is a great number of different motors (and manufacturers) with particular specifications. This is where manufacturers of planetary gears show their degree of flexibility. Basically, all IMS Gear planetary gears can be adapted to fit all motors available on the market; individual solutions are possible at the input and output sides.
How Relevant Are “Operational Dynamics” and “Gear Backlash” for Planetary Gears?
High levels of operational dynamics are achieved through low inertia torques, smooth running and low levels of mechanical wear. When it comes to designing and manufacturing planetary gears, IMS Gear uses plastic instead of metal for the planetary wheels where appropriate and technically feasible. This delivers low inertia torques. If necessary, we achieve smooth running through high-quality needle bearings or low friction coefficients between metal and plastics, low levels of mechanical wear through a special gearing design and the use of plastics wheels. In a nutshell: The material mix typical of IMS Gear ensures excellent operational dynamics.
In this context, the gear backlash of the planetary gear has to be considered. It depends on many factors: Type of load, number of stages, bearing, version, combination of materials. When seeking to compare different manufacturers, always remember that here, too, there are no standardized measuring methods.
Depending on the field of application, the efficiency of planetary gears is also to be specified. The gearing efficiency only takes account of the rolling motion of the gearwheel, the gear efficiency of all losses of the entire bearing. It is inevitably lower than the gearing efficiency. As there are no standardized measuring methods, a comparison of the efficiency levels of different manufacturers always requires special attention. Please contact us if you have any special requirements here.
Which Temperature Ranges Can Planetary Gears Be Used in?
The application resp. operating temperature range of planetary gears depends on the respective application but also on the material and lubrication. Our pure metal versions with standard lubrication range between −30° and +120° C, the Eco Series made of plastic between −15° and +65° C.
Which Protection Classes Do Planetary Gears Have?
The protection classes of planetary gears are defined according to DIN EN 60529. Planetary gears (short: PLGs) from IMS Gear can fulfil the following protection classes:
- Gears with sintered bearings: IP 40
- Gears with ball bearings (2 RS): IP 53
Upon request you can obtain output and motor gaskets to realize higher protection classes.
Which Installation Position Is Possible for Planetary Gears?
Due to grease lubrication the IMS Gear planetary gears can be installed in any desired position. In vertically arranged outputs, additional sealing measures can be provided on request.
What Is the Service Life of Planetary Gears?
Depending on environmental conditions and the operating data of the drive system, the service life of a planetary gear ranges between 200 and 30,000 hours. The great variety of application options precludes any generally applicable forecast of service life.
Planetary gears from IMS Gear are usually lubricated with grease and therefore maintenance-free during their service life. Depending on the requirements profile, we select the optimum lubricant from more than ten options.
The structural conversion through the hardening of the individual metal parts has a positive effect on the strength and wear behavior. IMS Gear has its own heat treatment shop. As the entire metal manufacturing is in-house, we can choose from various steels for hardening.
How Noisy Are Planetary Gears?
Low-noise behavior is a decisive criterion for certain applications of planetary gears. In these cases, so-called low-noise planetary gears are the solution of choice. To achieve an optimum noise behavior, increased demands on concentricity and axial run-out of the motor end plate, flange and shaft need to be met. Axial forces act on the motor shaft due to helical gearing. Sufficient dimensioning of the motor shaft bearings should be taken into account here.
To counteract the grease-promoting effect of helical gears, radial shaft sealing rings or sealed motor bearings can be used. Especially in the field of low-noise planetary gears we from IMS Gear have developed extensive experience and are available as a reliable manufacturer and development partner.