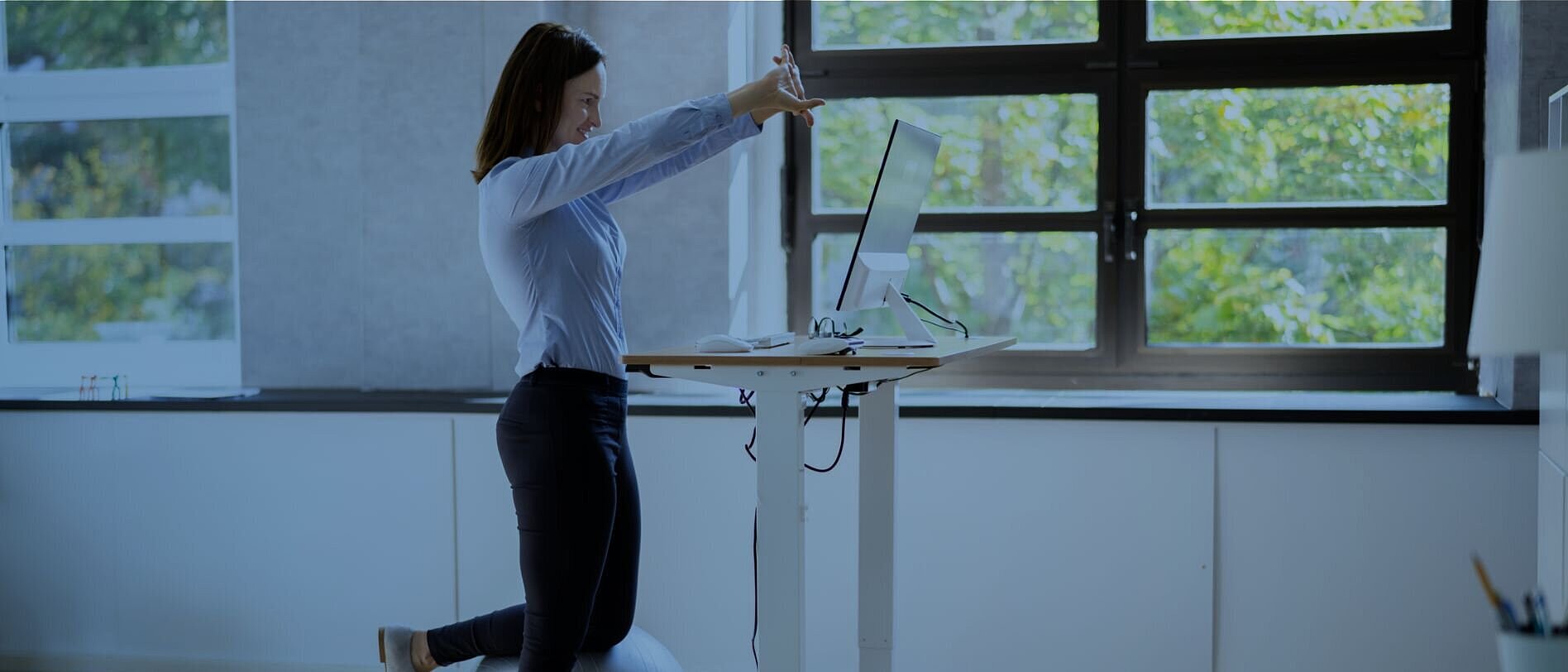
Planetengetriebe für Tischhöhenverstellung
Das hat NiveauDie Ergonomie an Arbeitsplätzen
Die Ergonomie an Arbeitsplätzen ist in den vergangenen Jahren zu einem immer wichtigeren Thema geworden. Die SUSPA GmbH aus Altdorf bei Nürnberg, Spezialist für Verstellsysteme, setzt bei innovativen Lösungen für die Höhenjustierung von Werkbänken, Küchen oder Arbeitsplätzen auf ein Planetengetriebe von IMS Gear. Die Lösung hat Niveau, denn die passende Höhe lässt sich nunmehr schnell, leise und komfortabel einstellen.
IMS Gear spannt mit seinem Baukastensystem den Bogen von der schnellen Qualitätslösung über kundenspezifische Anpassungen bis hin zur ausgefeilten Sondergetriebekonfiguration. So auch bei unseren Lösungen für moderne Agrartechnologie.
- Kompakter Bauraum
- Geringe Geräuschentwicklung
- Hohe Flexibilität & Anwendungsbreite
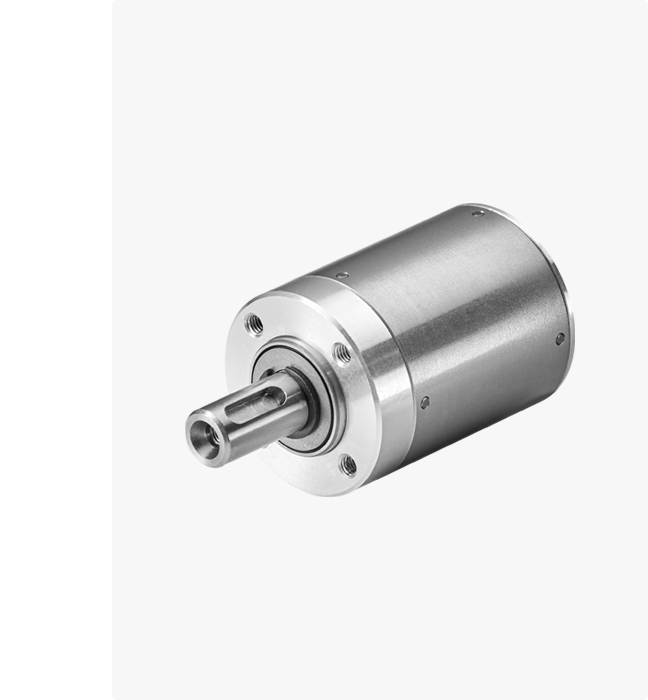
"Unsere Idee: Was im Automobilbereich erfolgreich umgesetzt wurde, lässt sich durchaus auf andere Anwendungen wie den Arbeitsplatz oder die Küche übertragen."
Von der Straße hin zum Arbeitsplatz
SUSPA und IMS Gear arbeiten seit Jahrzehnten erfolgreich zusammen. Unsere Planetengetriebe finden sich beispielsweise in Spoilerverstellungen von Mittel- und Oberklasse-Fahrzeugen diverser Hersteller. Ab einer definierten Geschwindigkeit fährt die Abtriebshilfe automatisch aus. Angetrieben wird das System von einem Elektromotor, dessen hohe Drehzahl von einem IMS Gear-Planetengetriebe in die benötigte Kraft umgewandelt wird. Die Lösung aus dem modularen Baukastensystem benötigt geringen Bauraum, und dies hat die SUSPA-Ingenieure auf die Idee gebracht: So müsste sich doch auch eine elektrische Höhenverstellung für zahlreiche Anwendungen im Home- und Industriebereich konstruieren lassen. Gedacht – gesagt – getan!
Vom Heckspoiler zur Tischverstellung
Als Ausgangspunkt wurde die Motor-/Getriebelösung der Spoilerverstellung gewählt. Da der Bauraum im bislang hydraulisch angetriebenen Movotec Spindel-Motor-System (SMS) auf 35 Millimeter Außendurchmesser begrenzt ist, musste das Getriebe angepasst werden. „Statt einer axialen Verschraubung wurde eine radiale Laserverschweißung umgesetzt. So konnte der Außendurchmesser von 32 auf 28 mm reduziert werden.“ erklärt Helmut Brugger, Vertriebsingenieur IMS Gear. Dies wird durch die Variabilität des IMS Gear-Baukastens ermöglicht, ohne dass in die Verzahnungsgeometrie eingegriffen werden muss. Anders als beim Einsatz im Heck eines Fahrzeugs ab 100 km/h in direkter Nachbarschaft eines soundstarken Motors kommt es bei der Verstellung eines Arbeitsplatzes stark auf die Minimierung des Geräuschpegels an. „Deshalb sind beide Stufen des Getriebes mit Kunststoff-Zahnrädern ausgeführt. Die Planetenträger sind angesichts der hohen Belastung aus Metall hergestellt“, erläutert Brugger.Die Entwicklungszeit, inklusive der kompletten Validierung des neuen Produkts mit einer solch hohen Leistungsdichte, sollte so gering wie möglich gehalten werden. Deshalb war es von Vorteil, dass auf den modularen Getriebebaukasten von IMS Gear zurückgegriffen werden konnte. Die kurze Zeitspanne für ein passgenaues Getriebe ist nur durch den Einsatz von in Großserie vorgefertigten Verzahnungskomponenten von IMS Gear möglich gewesen.
Nachteile herkömmlicher Systeme ohne Leistungseinbuße überwinden
Ausgangspunkt der neuen Anwendung war der Gedanke, die bisher dominierenden Gasdruckfeder-Systeme abzulösen. Deren Nachteile liegen unter anderem im größeren Bauraum, schlechterer Justierbarkeit und damit insgesamt erhöhtem Integrationsaufwand. SUSPA geht davon aus, dass elektrische Systeme sich sukzessive durchsetzen werden. Insofern bewegt man sich auf die Großserie zu. Auch in diesem Projekt zeigte sich die Rolle von IMS Gear als Möglichmacher für Kunden: Der Rückgriff auf ein modulares System eröffnet viele Vorteile für den Anwender: Es besitzt die Variabilität, verschiedenste Einzelteile aus Metall und Kunstsoff zielführend zu unterschiedlichen Untersetzungen zu kombinieren. Die Qualität und Haltbarkeit all dieser Teile wurde bereits in zahllosen Testläufen und Serieneinsätzen nachgewiesen. So bietet IMS Gear Auslegungs- und Produktionswissen aus der Großserie auch für kleinere Anläufe. Am konkreten Beispiel der Höhenverstellung: In der ersten Stufe trifft die hohe Drehzahl des Elektromotors direkt auf das Getriebe. Dort sorgt nun eine geräuschmindernde Low Noise-Schrägverzahnung aus Kunststoff für die erste Untersetzung bei noch geringem Drehmoment. „Die genaue Umsetzung der speziell entwickelten Verzahnung in dieser Stufe basiert auf der jahrzehntelangen Erfahrung von IMS Gear, gepaart mit modernsten Simulationsberechnungen“ erläutert Brugger. In der zweiten Stufe wandeln geradverzahnte Kunststoffräder die Drehzahl in das benötigte Drehmoment um. Das elektromechanische Movotec Spindel-Motor-System (SMS) von SUSPA bewältigt zusammen mit der IMS Gear-Getriebetechnologie hohe Hebelasten von bis zu 150 kg pro Hubsäule. In jedes Hubelement, das einen Profilquerschnitt von nur 35 Millimeter aufweist, wurde ein DC-Elektromotor mit dem geräuscharmen IMS Gear-Getriebe integriert, das eine ebenfalls innen liegende Spindel dreht. Durch die rotatorische Bewegung verfährt die drehgesicherte Spindelmutter in axialer Richtung. Sie ist direkt mit dem Führungsrohr verbunden, das auf diese Weise je nach Hublänge um 150 bis maximal 400 Millimeter ein- und ausgefahren werden kann.
Fazit
Der modulare Ansatz von IMS Gear hat durchgängig dazu beigetragen, den zum Teil konkurrierenden Anforderungen des komplexen mechatronischen Gesamtsystems gerecht zu werden. Die Fähigkeit, aus dem Baukasten heraus insbesondere zeitnah Änderungen für neue Lösungen zu generieren, wurde hier erneut unter Beweis gestellt. Sollten zum Beispiel in Zukunft höhere Lasten zu bewältigen sein, ließe sich dies aus dem Baukasten heraus umsetzen. Beispielsweise mit stärkeren Planetenrädern aus Metall oder einer anderen Untersetzung. „Modulares System bedeutet hier ganz konkret: Kürzere Time-to-Market und wirtschaftliche Vorteile, weil Lösungen den tatsächlichen Anforderungen angepasst werden können“.
Sie suchen eine passgenaue Lösung für Ihre ganz eigene Anwendung? Dann lassen Sie uns darüber sprechen: Als erfahrener Entwicklungspartner sind wir bei IMS Gear immer gerne mit dabei, wenn es darum geht, neue Lösungen für die Welt von morgen zu entwickeln.
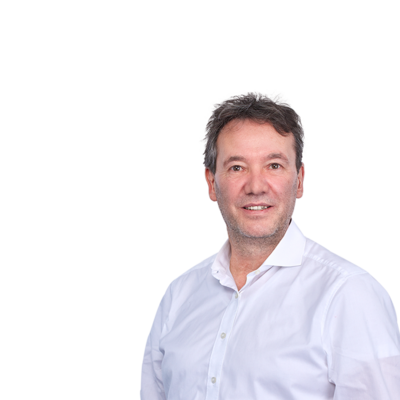